機械社區(qū)
標題: 應用solidworks flowsimulation進行基于鉑金攪拌器結構強度的對比分析 [打印本頁]
作者: 寂靜天花板 時間: 2016-6-6 19:03
標題: 應用solidworks flowsimulation進行基于鉑金攪拌器結構強度的對比分析
攪拌器在進行熔融玻璃攪拌時,受力情況較為復雜,無法直接估算。當我們對攪拌器的結構強度進行分析時,施加邊界條件就比較困難。因此,我們采用耦合分析的來解決這個問題。
因為玻璃熔融狀態(tài)下,是一種流體狀態(tài)。因此,我們首先使用SolidWorksFlow Simulation進行流場分析獲得攪拌器上的受力情況。然后,我們利用SolidWorks FlowSimulation與SolidWorksSimulation之間的接口,將流場計算得到的受力條件導出來作為邊界條件,對攪拌器進行結構強度分析。先后進行了三個個設計方案的橫向對比。列表如下:
方案1
攪拌器采用菱形截面的型材
壁厚2mm
7.970 Kg
方案2
攪拌器采用圓形截面的型材
壁厚2mm
7.917 Kg
方案3
攪拌器采用圓形截面的型材
壁厚1.5mm
7.662 Kg
我們對兩種攪拌結構進行了流場分析和結構強度分析,并對比了兩者之間的區(qū)別。從對比結果看,在給定的條件下,為圓形截面攪拌器應力水平更低,因此,我們接下來針對這種結構,減薄了壁厚,再次進行強度分析。并對比了壁厚調整前后的應力水平。
熔融玻璃的流場分析,目前的研究進展一般假設玻璃液為均質牛頓型粘性流體

,同時,攪拌過程中玻璃液的溫度基本不變,因此,我們考慮采用的等效玻璃液參數(shù)為:密度2200Kg/M3,動力粘度150Pa.s。
方案一采用菱形截面的攪拌器。我們首先對其進行了流場分析。流場分析的模型如下圖所示:
% }" c, c! Y) {1 n/ H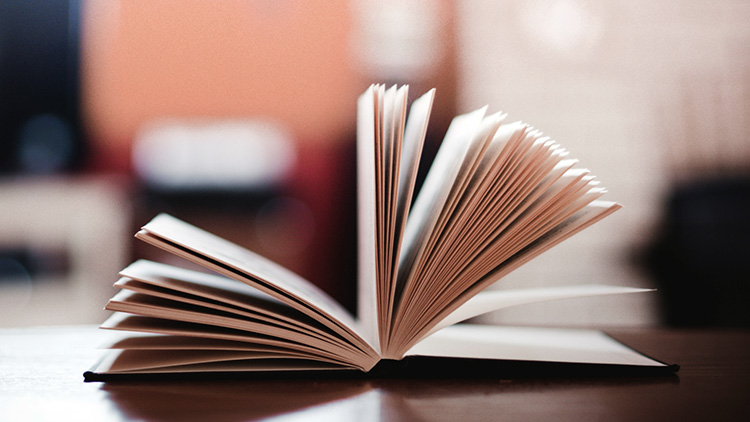
在流場分析時,我們給定坩堝中充滿了玻璃液,并設定攪拌器的轉速為45rpm,進行分析計算。計算得到的流場流線圖如下圖所示。
* {) n) ]& _5 w; z! M% H& ~攪拌器上的承受的壓力分布圖如下圖所示:
5 @' F/ m7 }- Z4 ~; W
從流場分析的結果中我們還可以輸出給定條件下,攪拌器上承受的扭矩,如下表:
通過流場分析,我們能夠直接將流體分析的結果導出到SolidWorks Simulation中,作為邊界條件,對攪拌結構進行結構強度分析。
之后,我們可以建立針對攪拌器的結構分析算例,在其中,我們只需設定相應的邊界條件,然后即可劃分網格并進行仿真了。在材料數(shù)據(jù)方面,我們得到了鉑金高溫下的機械性能,因此,采用高溫鉑金的材料特性數(shù)據(jù)進行本次計算。從結果對比的角度,只要幾個設計方案的材料數(shù)據(jù)都取為一致,這樣做出來的對比結果還是有意義的。我們使用的材料數(shù)據(jù)如下:
7 ]8 H- x- C* G9 Z$ a* m7 {' wPt
密度(g/cm3,20℃)
21.45
比熱[J/(kg·K),20℃]
131.2
導熱率[W/(m·K),0~100℃]
73
線膨脹系數(shù)(K-1×10-4)
9.1
彈性模量(N/mm2)
1.72×105
泊松比
0.39
為了獲得較好的結果,我們采用3mm的單元大小進行網格劃分。共劃分單元122294個,局部網格單元如下圖所示:
通過計算,我們得到了菱形截面攪拌器上的結構應力及位移結果。最大應力出現(xiàn)在菱形型材與圓柱相交的位置,大小為40.2Mpa,但考慮到此處為理想尖角位置,存在應力奇異,因此此處的應力是偏高且不收斂的,實際的應力猶豫存在焊縫過渡,應力水平應該低一些。另外,在攪拌框形結構上方,存在應力梯度較大的位置,此處的應力約為16MPa左右。在1300度高溫的情況下,鉑金屈服強度39.5MPa。因此,在給定條件下,方案1攪拌器整體還是安全的。局部可能接近屈服。
下圖顯示了變形結果。攪拌器在給定條件下,產生彎曲與扭轉相結合的變形,其中,攪拌器扭轉變形圖如下圖所示:由于攪拌器框形部分受到玻璃熔液的約束作用,變形較小,最大扭轉出現(xiàn)在攪拌軸頂端。
4.2 方案2分析結果方案2的攪拌器結構基本不變,只是將菱形截面換成了圓形截面,壁厚2mm。這種方案的重量和方案1相比重量輕了53克,重量基本相同。我們仍然首先對其進行了流場分析,玻璃液的參數(shù)與上面所述相同。流場分析的結果如下圖所示:
7 E3 G8 ^! m* ^( [9 C& b7 G從流場的分布圖來看,圓形截面的攪拌器,表面壓力分布更為集中,流線分布顯示速度的均勻性稍差。從扭矩情況看,方案2受扭矩與方案1基本一致。
采用同樣的技術,我們將流場分析的結果導出到Simualtion中,對方案2進行了結構分析。
我們采用4mm的單元大小,總共劃分了55683個單元,局部網格圖如下圖所示:
方案2的應力分布情況表明,最大應力出現(xiàn)在攪拌器框形與軸的交匯處,應力為28.3mm。但此處為理想尖角位置,存在應力奇異現(xiàn)象,實際應力應當偏低。而攪拌器框形上方出現(xiàn)應力梯度較大位置,此處應力約為14MPa左右。
變形分布云圖如下圖所示,變形趨勢與方案1是類似的,最大扭轉出現(xiàn)在攪拌器上端。
考慮1300度高溫時,鉑金的屈服強度為39.5MPa,方案2攪拌器整體是安全的。
4.3 方案3分析結果通過方案2的計算,我們可以得出結論,在給定條件下,方案2結構強度和剛度比方案1稍好。并且還有一定的安全裕量。因此,我們考慮是否能夠通過減薄圓形截面壁厚,來減少貴金屬的使用量。
基于這種考慮,我們將方案2的圓形截面壁厚減薄到1.5mm,并按照同樣的條件進行結構有限元計算,并將結果與方案2進行對比。由于方案3的外形尺寸與方案2完全一致,因此,流場計算的結果就可以通用,不需要再計算了。
由于壁厚減薄,為了獲得精確結果,我們采用2mm單元大小進行網格劃分,共得到單元數(shù)量357723個,局部的網格圖如下:
計算得到的應力結果表明,最高應力有所上升,但仍然在安全范圍內。最大應力仍然出現(xiàn)在攪拌框與軸交界處,攪拌框上部同樣出現(xiàn)應力梯度較大區(qū)域,改區(qū)域的應力約為14~16MPa。
從變形結果來看,壁厚減薄之后,扭轉變形略有上升。最大變形量約為0.58mm。
5 結論通過上面的討論,我們可以得出結論,在給定條件下,菱形截面的攪拌器強度和剛度稍弱,圓形截面的攪拌器強度和剛度較好。在壁厚減薄之后,圓形截面的攪拌器仍然比菱形截面的攪拌器要好。我們將對比結果列表如下:3 D' y6 o ~3 k: W# R, w! I
7 x2 {, I% N+ v
方案
結構描述
壁厚
最大應力
質量
方案1
攪拌器采用菱形截面的型材
壁厚2mm
40.2Mpa
7.970 Kg
方案2
攪拌器采用圓形截面的型材
壁厚2mm
28.3Mpa
7.917 Kg
方案3
攪拌器采用圓形截面的型材
壁厚1.5mm
33.7Mpa
7.662 Kg
3 i Y# w+ q) l: z2 c通過對比,我們認為在給定條件下,圓形截面的攪拌器強度和剛度相對更好。
作者: 漫步z云端 時間: 2016-6-6 23:40
很好,正在用simulation學習了,謝樓主分享!
作者: 極限思維 時間: 2018-5-10 13:06
牛
作者: 亂月殘風 時間: 2018-10-4 13:08
???????????????
作者: 亂月殘風 時間: 2018-10-4 13:08
9
歡迎光臨 機械社區(qū) (http://mg7058.com/) |
Powered by Discuz! X3.4 |